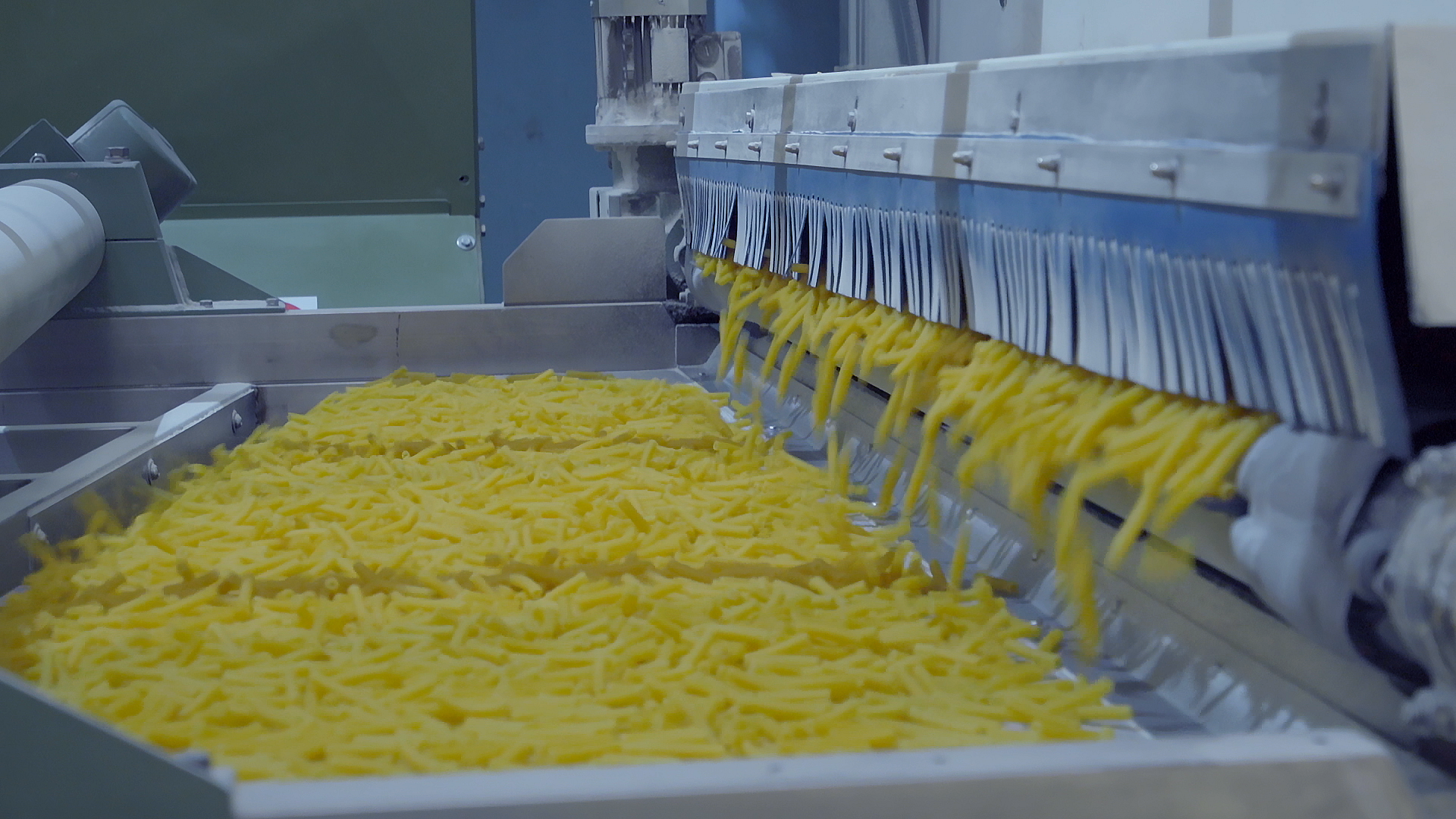
CASE Videojet
Pasta maker Di Martino improves uptime with Videojet and KPN
Every pasta lover knows the colorful packaging of pasta maker Di Martino, with its typically Italian illustrations, along with indispensable markings and codes. After all, without these apparently minor details the products could not be distributed. The marking and coding equipment of Di Martino is therefore now available 24/7, thanks to the Customer-Independent Cellular Network of Videojet and the premium connectivity of KPN.
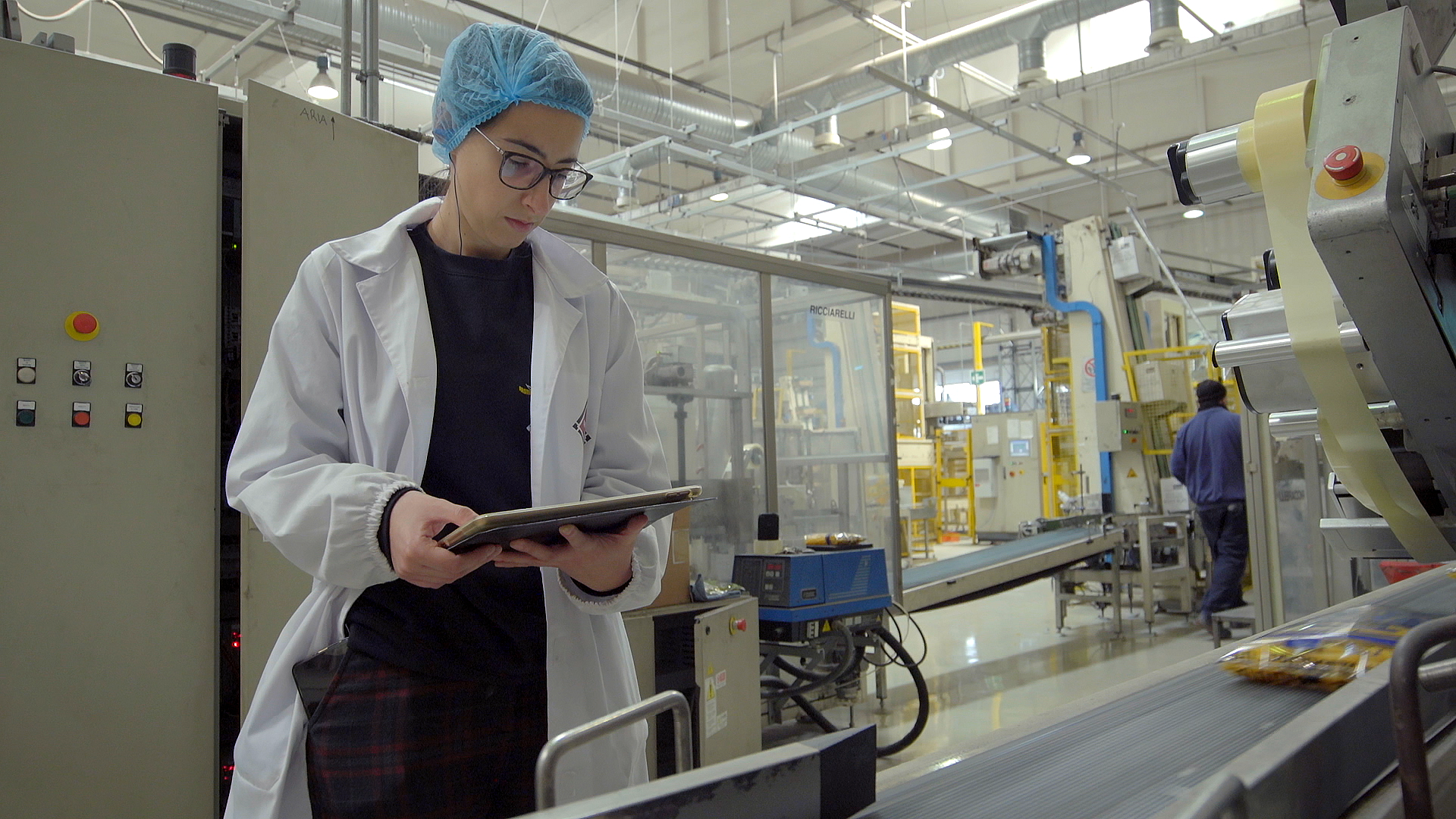
Essential equipment for Di Martino’s production process
Pastificio Di Martino is a pasta maker in Gragnano, an Italian village known for its perfect pasta. Giuseppe Di Martino opened the factory there in 1912. Now, more than 100 years later, the family business is still located in the pasta capital of Italy. The company produces more than 120 types of pasta that are sold in 35 countries, often in colorful packaging with illustrations by the Italian fashion house Dolce & Gabbana. Needless to say, that packaging not only has to look good, but also needs to contain the right markings and codes. For instance, the production and use-by date, bar codes, batch numbers and the name of the importer must be clearly visible.
Di Martino uses the industrial marking and coding solutions of Videojet Technologies for that purpose. That equipment has to be available 5 days per week, 24 hours per day. Any downtime of that equipment has a direct effect on the logistical process: the pasta cannot leave the factory without the markings. Products that have not been properly coded, marked or printed are rejected or have to be printed again – which delays delivery.
You can see in the video below how Videojet and KPN contribute to the uptime of Di Martino:

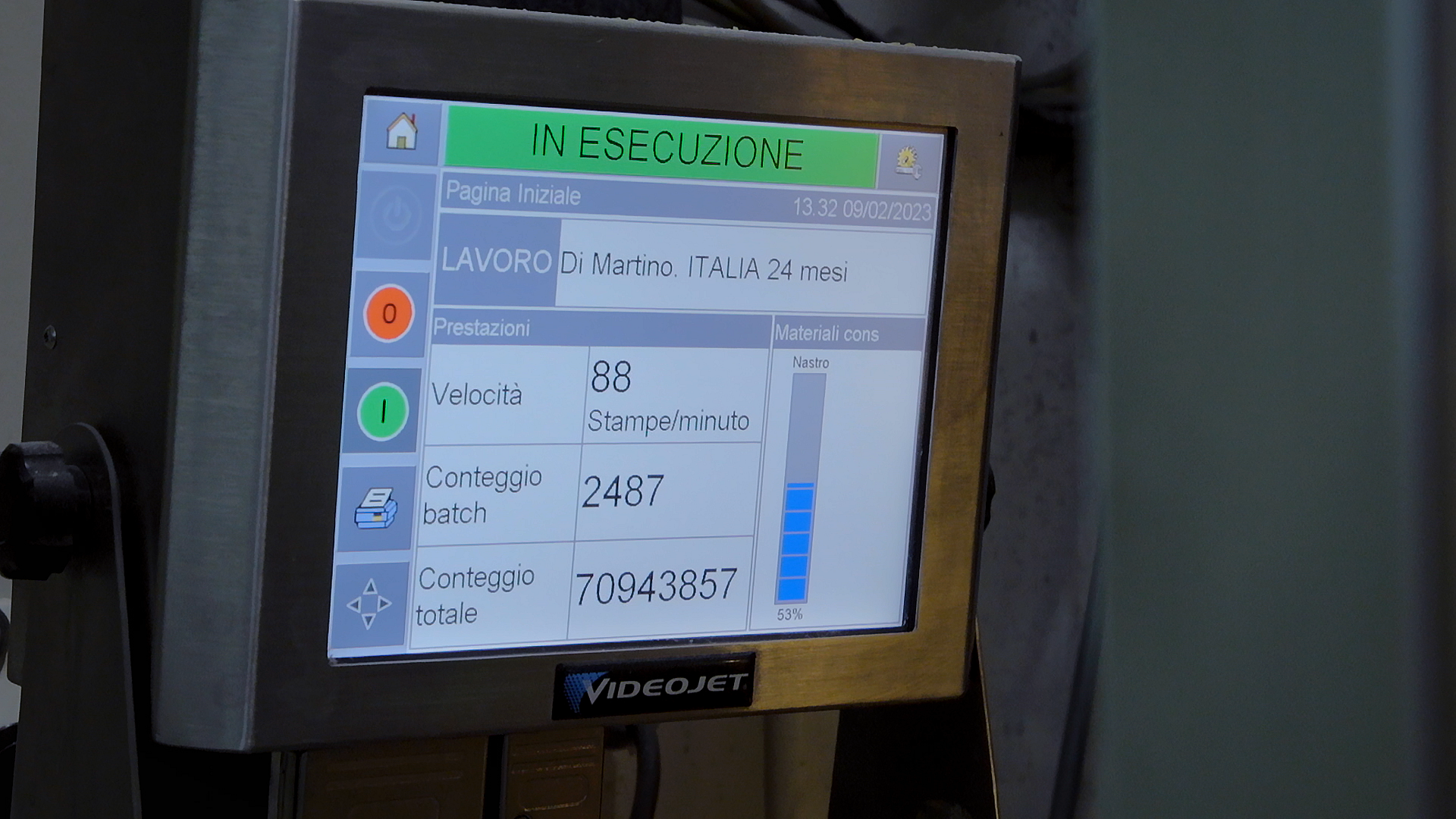
Remote Monitoring
Unplanned downtime has a big impact on costs as well. It has cost Di Martino thousands of euros in the past. One of the solutions for preventing this is to monitor the equipment with the VideojetConnectTM Remote Service, a cloud-based solution via the local company network, which gives real-time information about printers. But the internal IT policy of Di Martino does not permit that.
This is a restriction that Maurice Janssen Duijghuijsen, KPN VP Sales IoT & Data, comes across frequently. It is a way in which companies protect themselves against external risks. “Connecting the equipment to a WiFi network managed by the customer is not always an option either. It requires coordination with the customer’s IT department, and you are then dependent on the signal from the existing WiFi network, which might be unstable.”
KPN Things Router
The alternative is an industrial router, which is connected via the mobile IoT network to the coding and marking solutions of Videojet. KPN IoT offers a total solution: the KPN Things Router. A preconfigured solution that combines the global connectivity of KPN IoT with the IBR200 4G/5G routers of Cradlepoint. This enables Videojet’s customers to monitor their equipment remotely, prevent downtime and safeguard their continuity, without impacting the local network.
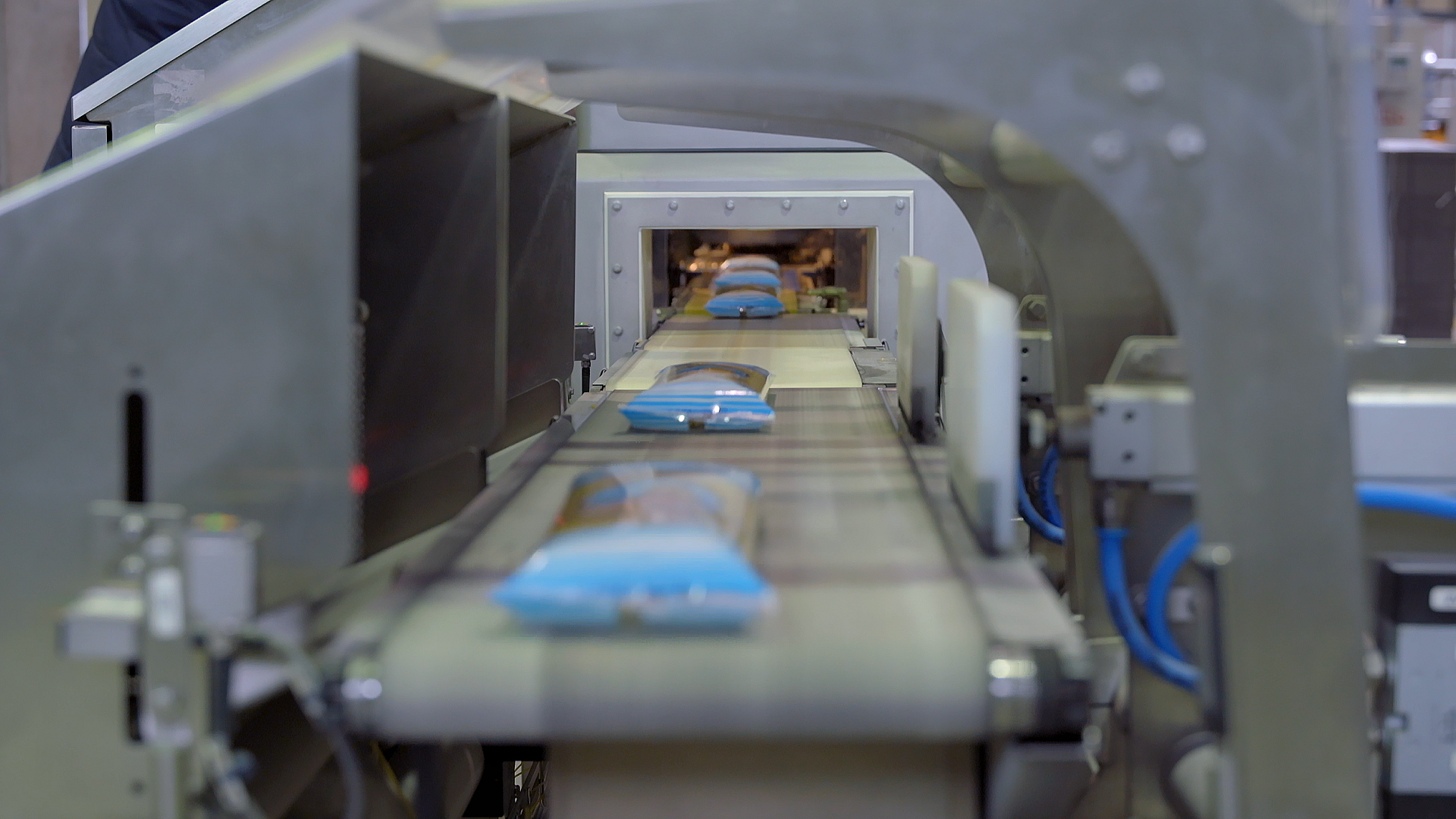
Connection anytime, anywhere
That was the case with Di Martino too. The pasta maker implemented a Videojet Customer-Independent Cellular Network (CICN), a mobile network that makes use of the routers of Cradlepoint and is independent of the existing company infrastructure. The Videojet printers make a wireless connection with this 4G LTE network.
KPN’s premium connectivity ensures that the Videojet printers are connected to the VideojetConnectTM Remote Service cloud, anytime, anywhere. “Thanks to the partnership with KPN, Videojet is no longer dependent on the quality of the customer’s WiFi or wired network”, says Jean-Paul Cohen, Commercial Director Western Europe at Videojet Technologies. “And as KPN operates internationally with its partner Capestone, Videojet can offer its customers in Europe and elsewhere top-quality connectivity and remote support.”
Major cost saving
The solution of Videojet and KPN is a hit with Di Martino. Since the company has been using the VideojetConnect Remote Service via the CICN, the unplanned downtime has declined by 20 hours per month. The cost saving is in excess of €50,000 euros per year.
Luisa Mazza, Quality Manager at Pastificio Di Martino, is therefore full of praise for the solution provided. “The positive experiences - both with the advanced technologies and with the service teams of Videojet and KPN - leave you wanting more, and we would certainly recommend them to other manufacturers.”